2003/08/25
包丁を作ろう!!
毎日料理をする日々です。
調理道具一式はもともとあったものですが、
包丁だけはいいものを・・・と、男らしく思っていました。
私が包丁に求めるものは・・・
1.絶対和包丁
2.材質は鉄系
3.出刃と刺身の中間ぐらい
万能包丁より細めの、すらっとしたラインの包丁がほしい
4.柄もかっこいいもの
と、基本的に見た目重視です。
ナイフマガジン 包丁の本などいろいろ探しては見ましたが
そんなもの存在していません。
和包丁も、もっと外観にこだわってくれればいいのにねぇ。
みんな柄が同じなもんで、いいものでも買う気になれなかったです。
そうなっては残る道はただひとつ
やっぱり自作しかありません。
そうはいってもそんな知識などひとつもない私にとって、
そんな勇気などありませんでしたが、ひとつの本が勇気をくれました。
ナイフマガジン No.80 2000/2 号
サブタイトル その名も「鍛造ナイフを作ろう」
そんなわけで、鋳造 アルマイト 削りだしを極めた?私の
最後の挑戦 鍛造に挑戦したいと思います。
鍛造ということで、デザインは簡単でかっこいいものを作ります。
元にしたデザインはこちら。
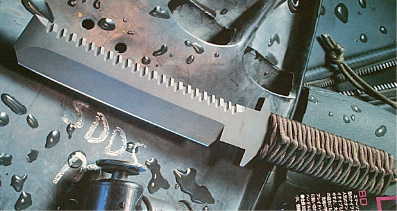
ストライダーナイフですが、柄は握りやすい木で
あごの部分はもうちょっと出し、包丁に近づけます。
詳しいやり方はナイフマガジンを参照しましょう。
私は根性で中古を見つけました。
(雑誌なのに定価が1000円もするんだもん)
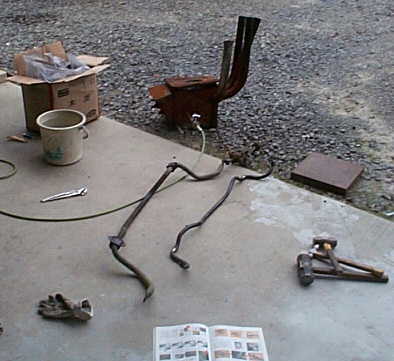
用意するもの
炭(左上 バーベキュウ用)
水 (バケツ 危険防止のため)
ウォーターポンププライヤー (ヤットコの代わり 材料をつかむもの)
七輪 (炭を入れるやつ 何でもいいので私は地球号を使用)
スタイビライザー (包丁の材料 バネ鋼ならスプリングでもいい)
叩き台 (普段板金で使ってる、鉄の板を使用)
ハンマー (これも普段使っているもの 3種類)
ナイフマガジン (見ながらやりました)
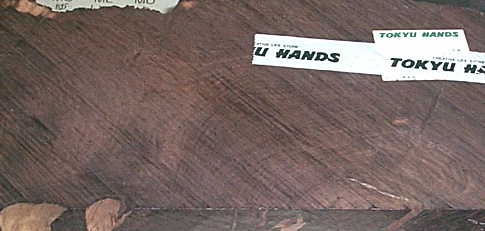
東急ハンズで買った、正体不明の木
800円でグリップに使います。
磨くとつやの出る、非常に硬い木です。
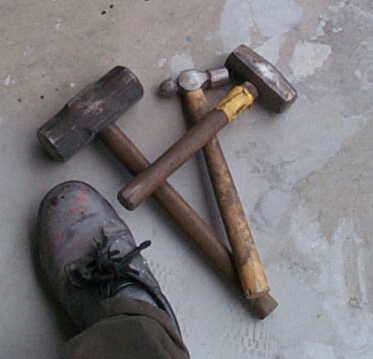
ハンマーはほとんどの作業を一番大きいのを使用。
小さいものはまったく歯が立ちませんでした。
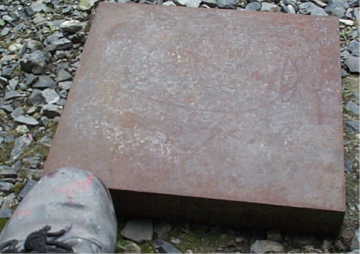
叩き台
重くないと意味がないです。
これで、20キロぐらいあると思います。
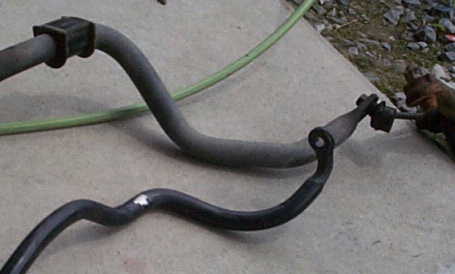
スタビライザー
レガシー用とマーク2用を拾ってきました。
太いほうのマーク2用を使おうと思い、必要な長さに
切ってみたんですが・・・
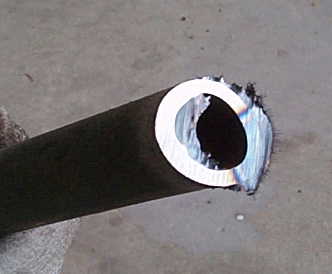
なんとパイプでした。
昔のクラウンは無垢だったんだけどなぁ。
そんなわけで、しかたなく細いレガシー用を使用しました。
さて、いよいよ鍛造にはいるわけですが
難しいことは何もありません。
鋼材の温度を700度から800度に上げて
ひたすらハンマーで叩くのみです。
そこまで温度を上げるのに、本では
七輪とドライヤー(送風)で火をおこすんですが
(その方法でアルミが解けるぐらいの温度まで上がる)
七輪をわざわざ買うのももったいないので
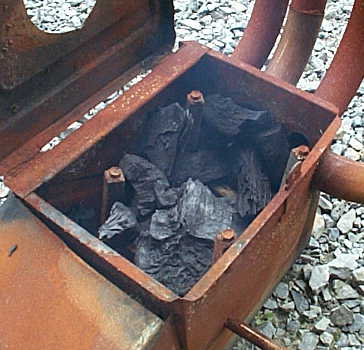
地球号に炭を入れて、コンプレッサーで空気を送ります。
これで十分温度が上がります。
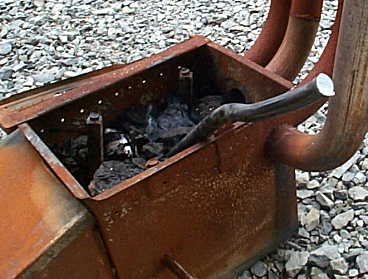
適当に切った鋼材をいれて加熱します。
10分ぐらいで赤くなってくるので、ひたすら叩きます。
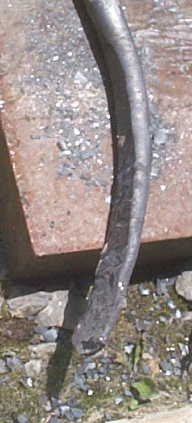
2〜3回 繰り返したところです。
恐ろしく疲れます。
一回で叩ける時間は20秒ほど。
その間に大ハンマーで力の限り叩きます。
その間当然無呼吸です。
真夏のくそ暑い日に、日向で、死にそうになりながら
何とかがんばりました。
予定より細い鋼材ですので、まげて太くしないといけません。
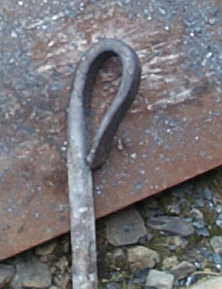
ここまでくるのに、さらに3回ぐらい。
ここからさらに3回ぐらいで・・・
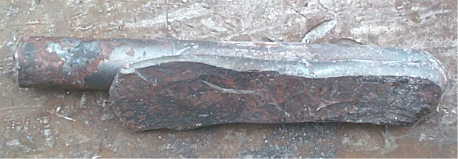
ここまでいきました。
そして、ここまできて気がつきました。
これを包丁の形に鍛造なんて、絶対無理です。
体力 時間 熱量 すべてが圧倒的に足りません。
あとから気がつきましたが、鋼材を鍛接する場合は
鍛接材と呼ばれる薬品が必要だそうです。
一番致命的なのは熱量で、この材を赤くするのに
非常に時間がかかります。
赤くなっても鍛造できる時間が極端に少なく、ぜんぜん形が
変わっていきません。
そこで、炉に廃油を加えてやってみましたが、これが大失敗。
直接高温部に当てないとまったく温度が上がらず、炉の中の
温度が不均一になり、一向に鍛造できません。
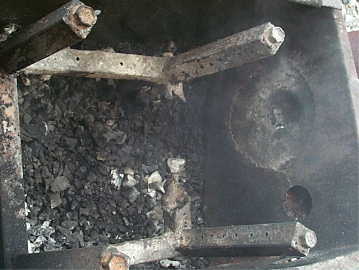
炉の中の、空気送りユニット。
炭の熱で溶けて、ばらばらになっています。
廃油で鍛造も不可能ではなさそうですが、専用の
炉を設計する必要があるみたいです。
そこで、計画も制作方法も変更します。
計画
「わたしも鍛造ナイフを作ろう」
材料
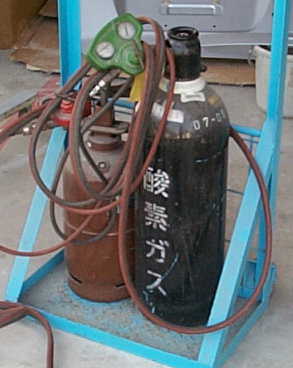
酸素バーナー
こ、こら! 誰だね?卑怯者とかいった人は?
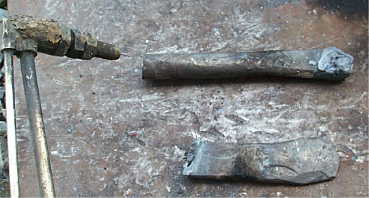
さっきの鋼材から、酸素バーナーで平たい部分を切り出します。
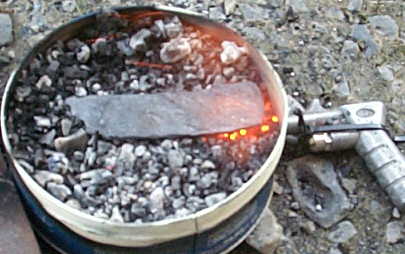
缶にさっきの炭を入れて、横に穴をあけて、そこからエアガンで
空気を送って簡易炉にします。
しかしこれはあくまで補助で、メインの熱源は酸素バーナーです。
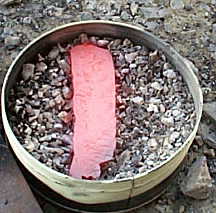
こんな感じに暖めて、ひたすら叩きます。
本当なら刃の部分も外形もこの時点でたたき出しますが、
どうやっても思い通りの形にはならないので
あとで削って形をあわせることにします。
大体の形はできましたので、「焼きなまし」をします。
これは、赤くなった鉄をできるだけゆっくり冷ますことで
鉄がやわらかく、加工しやすくする熱処理のことです。
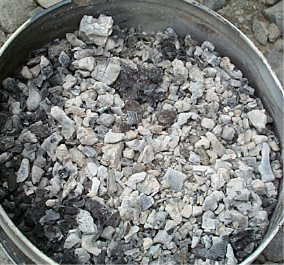
赤くした鉄を炭の中に入れて、1日かけて冷ましていきます。
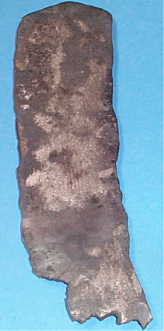
これが出てきたものです。
なんとも不恰好ですが、ここから削って形を合わせるので
板状のになっていれば、後はどうとでもなります。
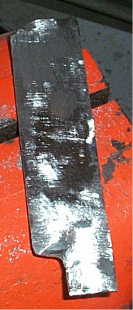
外形を削り、裏面だけは削って平らにします。
表面は鍛造の雰囲気を出すため、酸化皮膜を取るだけにします。
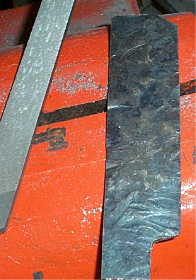
刃がまだついていませんが、とりあえずの形になりました。
これに適当な形の柄をつければ完成になります。
しかし・・・
はたして、このナイフはいつ使うんでしょうか?
どうせ作ったものなんだから、やっぱりいつも使いたいです。
ですが、この中途半端な大きさでは使い道が思いつきません。
そこで、またもや計画変更
「ポケットナイフを作ろう」
刃がグリップの中に折りたためるタイプで、
一番構造が簡単な肥後守タイプのナイフを作ります。
参考にしたものはやはりナイフマガジン 1999/8 号です
先ほどの材を、フォールディングナイフになるように削ります。
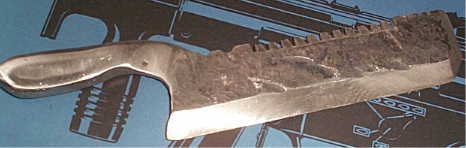
これで完成
下に突き出たところは厚さが足りなかったため、溶接で肉盛り
熱いうちにたたいて、何とか鍛造の面目を保っていますが
もうなんでもありです。
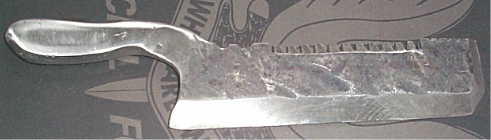
刃の後ろにはセレーションも切ってあります。
適当に刃をつけたところに、切断用の刃をつけた
ハンドグラインダーで切れ目を入れただけですが。
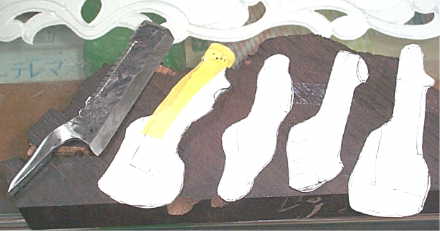
この刃を元にして、グリップの形を決めます。
結局4つ目で(左側)何とかうまくいきそうな形になりました。
グリップにあわせて、刃の尻尾の部分の形も変えています。
デザインの前に、大きさ的な制約が大きく非常に苦労します。
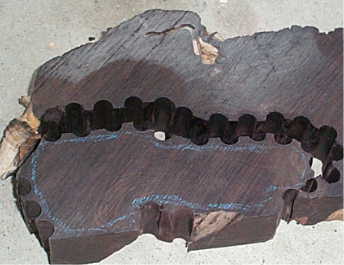
木から、グリップ部分を切り離します。
ドリルで穴を開けてつないでいきます。
が、こいつには致命的な弱点があります。
木の繊維の方向が違うんですね。
普通のグリップは木の板から切り出すと思いますが、
こいつは切り株の切れ端から切り出しています。
そのため強度的に不利ですが、何とかがんばります。
刃をつければ強度も安心ですが、それまでは
ちょっとの衝撃で割れそうです。
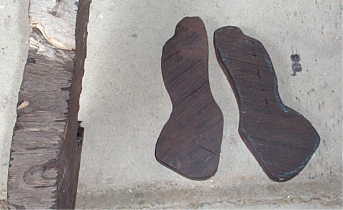
のこぎりで縦に半分に切り出します。
バンドソーがあればどれだけ楽なことか・・・
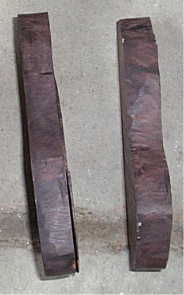
これでもちょっと分厚すぎるので、さらに縦に割らないとだめですね。
この材、ものすごく硬くて加工に苦労します。
普通の木ならこれぐらい簡単に薄くできるんですが・・・
この大体の形に削るのも、ペーパーでは無理で
グラインダーを使いました。
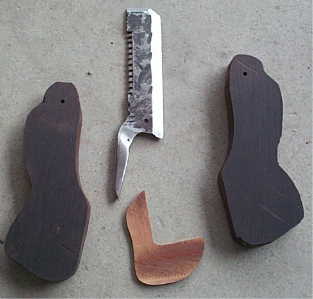
部品構成図です。
これを組み合わせて作ります。
一番下のは違う木から切り出したものです。
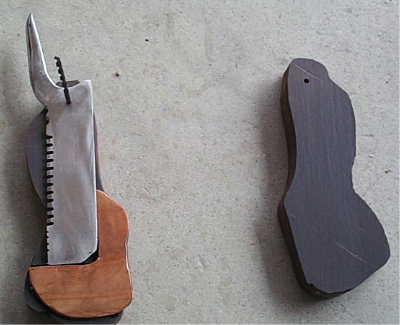
ナイフはこんな風に収まります。
このあとは木を接着剤でつけて、1日乾燥させます。
そのあとまたのこぎりで切っていきます。
が・・・
・
・
・
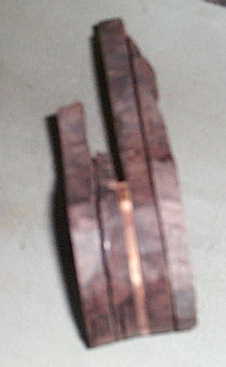
やってしまいました。
やっぱり折れちゃいました。
バンドソーがあれば一瞬の作業なのに・・・
板から切り出していれば、必要のない作業なのに・・・
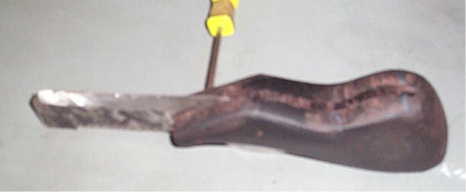
気を取り直して、今度はひとつの塊から切り出していきます。
残った材で作ったので、予定よりグリップが小さくなりました。
縦の割れ目はドリルとグラインダーで整形。
非常に気の遠くなるような作業でした。
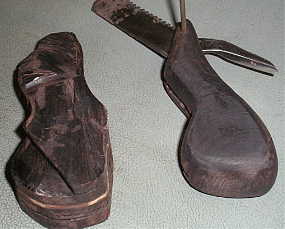
壊れたグリップと作り直したグリップ。
1作目が壊れたショックで、2作目はいいかげんに作りましたが
その割には結構いいものができました。
仮に組み立てて、合わせを確認していきます。
そしたら分離して、それぞれ仕上げにはいります。
刃ですが、今度は焼入れをします。
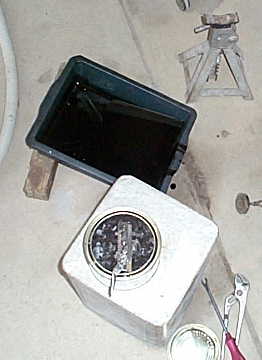
焼入れとは反対で、真っ赤にした後
オイルで急冷させます。
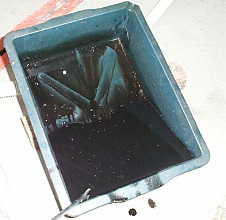
もちろん廃油を使用
酸素を使ったんで非常に簡単な作業でしたが、これだけで
ものすごく硬くなります。
さらに、このままでは硬くてもろいので
「焼き戻し」をして粘り強さも出します。
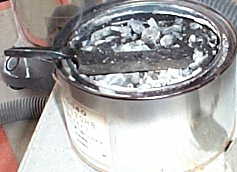
方法は180度ほどで1〜2時間ほかっておくだけです。
ホットプレートなどを使えば、時間も温度も簡単にできますが
めんどくさかったのでかなり適当です。
これぐらいかな?って温度に上げたあと
燃えカスの炭の中に突っ込んでおいて置きました。
ここまでくれば、後は仕上げのみ
砥石で刃をつけ、全体の酸化皮膜を取り
磨いていって完成です。
グリップのほうは、やはり強度不足でヒビが目立ち始めたので
全体をコーティングすることにしました。
いろいろ考えた挙句、FRP樹脂を塗ってみました。
そしたら恐ろしいことに、固まらないんです。
硬化剤の配合比を間違えたわけでもなく
(落ちた樹脂は固まっている)
いくら熱を加えても一向に固まる気配がありません。
木が硬化剤だけ吸っちゃったんでしょうか?
しょうがないのでシンナーで全部とります。
きれいに取れたからよかったですが、こんなところで
やり直しをするわけにはいきません。
そんなわけで、グリップはペーパーで磨くだけにします。
鉄に比べて簡単につやが出るので、600番程度で
光るから楽です。
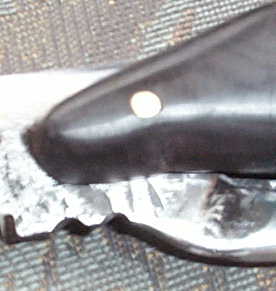
グリップと刃の固定は、3mmの真鍮棒をかしめるだけです。
棒を入れて両側からハンマーで叩くだけですが、いい感じで
固定できます。